Molten Metal Handling / Foundry Ladles
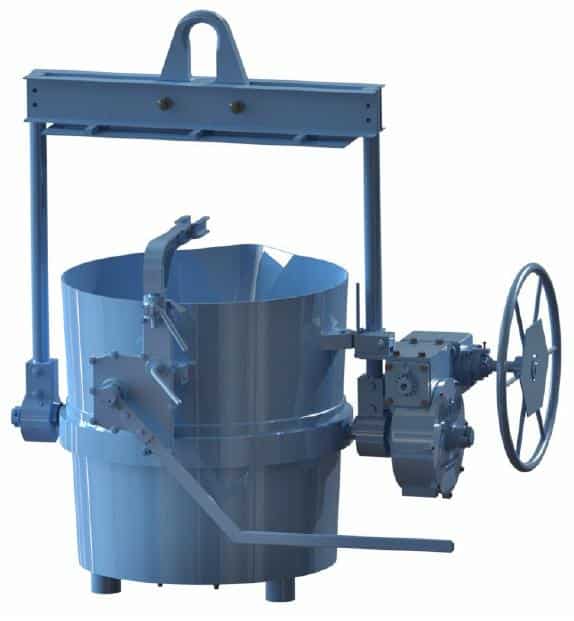
Series 1170 Precision Bottom Pour Ladles
Bottom pour ladles provide slag-free metal and are applicable for pouring both light and heavy work.
Design of the bottom-pour, rectangular, slide mechanism insures positive control over the flow of metal. With a housing, enclosing the machined rack and pinion, all moving parts are protected from foundry dirt, slag and sparks which tend to gum-up ordinary; open slides. The entire assembly remains clean. Manual fixtures, incorporated in the design, lock both the gooseneck and stop-per rod in their accurately, adjusted position. The entire mechanism is hinge mounted to the ladle bowl to permit ready adjustment of the stopper rod in its vertical alignment to permit ready adjustment of the stopper rod in its vertical alignment.
Slides can be furnished to release metal when lever is either raised or depressed. The dual motion of the lever applies whether lever is mounted to the right or the left of the ladle centerline. The broad flexibility in control over metal flow meets a wide range of conditions in varying foundry practices.
Disengagement of the bottom pour unit for maintenance purposes, is easily accomplished by removing the hinge pin.
Ladle bowls are well vented on the sides and bottom, to insure fast, safe drying of the linings.
Trunnion locations of geared, bottom pour ladles are engineered for correct balance. When ordering, specify linings to be used.
SIZE
0
CAPACITY
Series 1000 Covered, Tapered Ladles
No.1 Type (Lever) Shanks
Covered tapered ladle with No. 1 type lever shank and detachable ball.
Series 1010 Tapered Open Ladles
No.1 Type (Lever) Shanks
Open tapered ladle with No. 1 type lever shank, roller bearing trunnions and detachable bail.